
[ad_1]
3D printing has revolutionized manufacturing, enabling the creation of intricate shapes and buildings. Nonetheless, with regards to printing ceramics utilizing lasers, the method turns into more difficult. Researchers on the Swiss Gentle Supply (SLS) and the Paul Scherrer Institute (PSI) have damaged new floor by capturing 3D insights into this complicated manufacturing course of by tomography, shedding mild on the microscopic intricacies and providing potential for expertise enhancement.
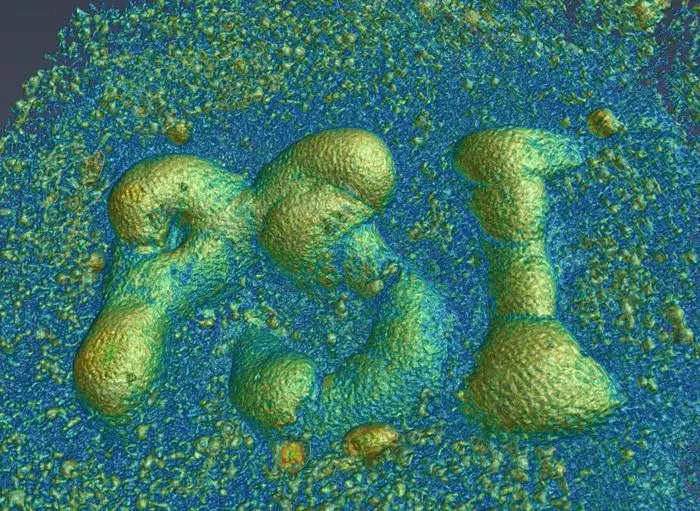
Conventional 3D printing, notably in aerospace, automotive, and medical industries, depends on laser-based powder mattress fusion (LPBF). LPBF entails layering superb powder on a substrate and melting it with a laser to type the specified form, repeated layer by layer. Whereas 2D X-ray photos have been used to check the method, the PSI researchers needed to delve deeper and visualize it in 3D.
Their breakthrough concerned utilizing aluminum oxide, a tough and brittle ceramic materials. Overcoming the challenges of speedy rotation and stopping materials dispersion, they efficiently tracked the printing course of in 3D. They used a high-speed digital camera and microscope to seize 100 3D photos per second, revealing the shocking habits of the soften pool.
The researchers’ strategy additionally allowed them to watch the formation of pores and hollows as the fabric solidified, essential for future functions. The findings maintain promise for enhancing LPBF expertise, although sensible functions could also be a way off.
Because the institute’s machine undergoes upgrades, the capabilities for finding out denser supplies with larger decision will broaden, additional advancing LPBF expertise.
Come and tell us your ideas on our Fb, Twitter, and LinkedIn pages, and don’t neglect to join our weekly additive manufacturing e-newsletter to get all the newest tales delivered proper to your inbox.
[ad_2]