![[INTERVIEW] Formnext 2023: scaling the manufacturing of technical ceramics with 3DCeram Sinto’s semi-automated manufacturing line [INTERVIEW] Formnext 2023: scaling the manufacturing of technical ceramics with 3DCeram Sinto’s semi-automated manufacturing line](https://bestnology.com/wp-content/uploads/2023/11/The-3DCeram-C1000-Flexmatic-at-Formnext-2023.-Photo-by-3D-Printing-Industry-1024x768.png)
[ad_1]
Throughout Formnext 2023, 3D Printing Business sat down with Maxence Bourjol, Gross sales Supervisor at ceramics 3D printing OEM 3DCeram Sinto, to study extra in regards to the firm’s semi-automated manufacturing line for technical ceramics.
By means of its suite of stereolithography (SLA) 3D printers, technical ceramic supplies, software program, and put up processing methods, 3DCeram purports to allow industrial scale manufacturing of ceramic components.
“One thing new that we actually wish to promote at 3DCeram is the power to make use of 3D printing not just for prototyping however for the mass manufacturing and mass customization of ceramic components,” defined Bourjol.
At Formnext, the Limoges-based firm additionally showcased CPS 2.0, the newly up to date model of its Ceramaker Printing Software program platform. Developed over the previous two years, this new software program has been designed to simplify and optimize the ceramic 3D printing course of for industrial customers.
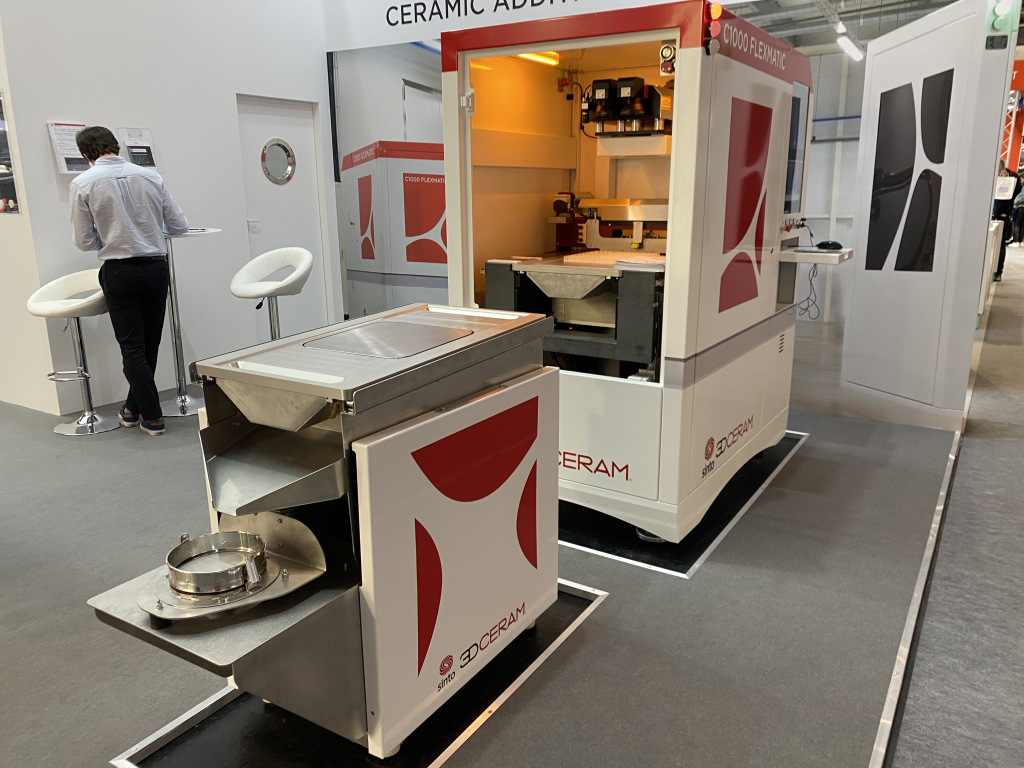
Scaling manufacturing with 3DCeram’s automated printing line
In accordance with Bourjol, the corporate’s printing line is essential to scaling productiveness. This manufacturing workflow integrates the corporate’s 3D printing and post-processing {hardware} right into a semi-automated manufacturing line.
“Mass manufacturing signifies that we aren’t solely targeted on the 3D printing step, however all levels of the printing line,” acknowledged Bourjol. “This implies 3D printing, post-printing, and semi-automation, which decreases wasted time between every step of the method.”

3DCeram’s SLA 3D printers have been designed with massive manufacturing runs in thoughts. The corporate’s C600 Final incorporates a construct plate measuring 600 x 600 x 300 mm. In accordance with Bourjol, this construct quantity can facilitate a manufacturing run of 80 components in simply 5 hours.
Furthermore, the C1000 Flexmatic 3D printer has reportedly been optimized to be simply built-in right into a semi-automated manufacturing setup. That is due to its detachable tank, which permits for in-line processing of 3D printed components.
While the size of every manufacturing run is closely depending on the scale of the half, Bourjol asserted that, for small components, “you possibly can simply have a whole lot of components on the printing platform.”
Nevertheless, Bourjol emphasised that the manufacturing scale of 3DCeram’s know-how just isn’t limitless. As an illustration, based on Bourjal, ceramics 3D printing won’t ever compete with the size provided by ceramic injection molding. “3D printing just isn’t made to supply billions of components,” defined Bourjol. “However it may be used for big batches of 1000’s of components.”
Bourjol highlighted the manufacture of semiconductors as being a notable software of 3DCeram’s printing line. Technical ceramics possess the required properties to satisfy the fabric necessities of those electrical parts.
As such, within the manufacturing of semiconductors, 3DCeram know-how is used to supply radiant tubes, wafer boats, gasoline induction ports, electrostatics chucks, nozzles and rings. The corporate’s SLA know-how may also 3D print ceramic heating parts used throughout thermal remedies. “They should produce a whole lot of components, so that they actually need our SLA 3D know-how for its massive 3D printing platform,” added Bourjol.
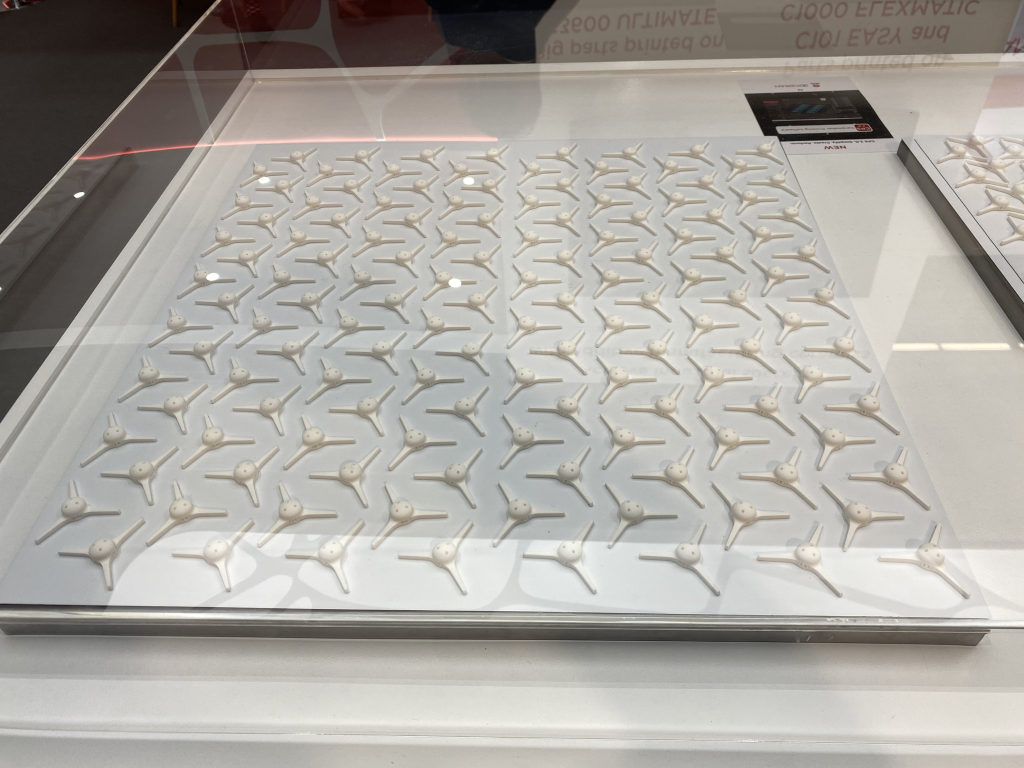
3D Ceram up to date to CPS 2.0
Bourjol additionally highlighted the important thing promoting factors of the just lately launched CPS 2.0 software program replace for 3DCeram’s Ceramaker Printing Software program. In accordance with Bourjol this replace was pushed by consumer suggestions from 3DCeram clients.
One key buyer request associated to creating the software program extra user-friendly. “Our software program was superb, however it might typically be difficult to make use of,” defined Bourjol. Subsequently, CPS 2.0 incorporates a brand new user-friendly interface and has been designed with the expressed purpose of simplifying the ceramic 3D printing course of. Furthermore, all 3D printing parameters are pre-loaded into the software program, decreasing pointless delays throughout the 3D printing course of.
This new replace additionally permits a number of 3D printers to be related to a singular software program interface. “We’ve got clients who’ve a number of 3D printers. What these clients need is to have one software program that may ship the 3D printing to all of their 3D printers,” defined Bourjol. “With CPS 2.0, it’s doable to attach our software program to as many 3D printers because the buyer desires.”
Moreover, Bourjol highlighted that CPS 2.0 permits customers to pick out from a spread of expertise ranges when utilizing the software program, optimizing the software program for all members of the manufacturing line. As an illustration, designers can entry design assist when selecting the 3D printing parameters, and 3D printer operators can entry designated assist when initializing the 3D printing course of. In accordance with Bourjol, this makes CPS 2.0 a “extra environment friendly instrument for patrons.”
Optimizing the manufacturing of inexperienced hydrogen
Trying to the long run, Bourjol pointed to 3DCeram’s ongoing efforts to leverage its know-how within the manufacturing of inexperienced hydrogen as a part of the European HyP3D Mission. The purpose of this mission is to showcase the viability of high-pressure Strong Oxide Electrolysis Cell (SOEC) know-how.
This five-year mission seeks to develop an ultra-compact, high-pressure SOEC stack able to changing electrical energy into compressed hydrogen. 3D Ceram’s position within the mission revolves across the manufacturing of zirconia Zr8Y components for the SOEC stacks. In accordance with Bourjol, these components can’t be manufactured utilizing typical strategies.
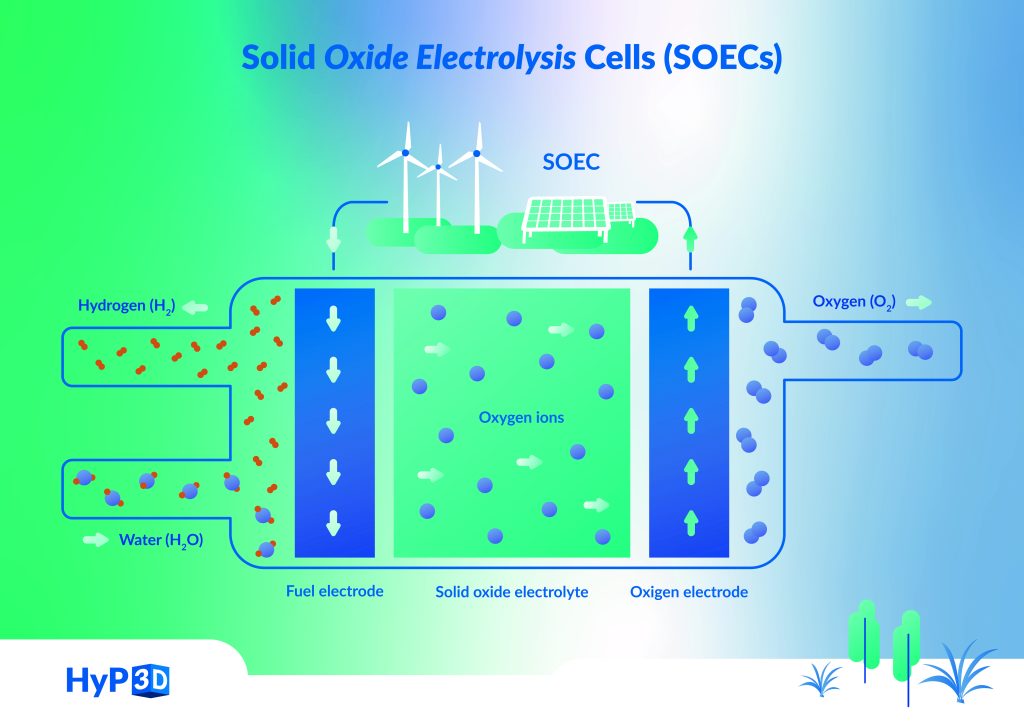
“With 3D printing, you are able to do some disruptive design with the intention to lower the scale of the components,” defined Bourjol. “Due to the complicated design, you may also enhance the effectivity of the half.”
Furthermore, Bourjol pointed to 3DCeram’s industrial-scale manufacturing capabilities as enjoying a significant position on this mission. “If all goes properly, this mission will transfer right into a manufacturing scale,” defined Bourjol. “This may require tens of 1000’s of zirconia components each month. So the request for the manufacturing of those zirconia components is totally enormous. This might be a highly regarded matter for us within the coming years.”
Subscribe to the 3D Printing Business publication to maintain updated with the newest 3D printing information. You can too observe us on Twitter, like our Fb web page, and subscribe to the 3D Printing Business Youtube channel to entry extra unique content material.
Are you curious about working within the additive manufacturing trade? Go to 3D Printing Jobs to view a choice of out there roles and kickstart your profession.
Featured picture reveals 3DCeram’s C1000 Flexmatic 3D printer at Formnext 2023. Picture by 3D Printing Business.
[ad_2]