
[ad_1]
US-based pure gasoline service supplier Upwing Power has leveraged know-how from steel 3D printer producer Velo3D to 3D print its Subsurface Compressor System (SCS) compressor module.
Through the use of Velo3D’s Laser Powder Mattress Fusion (LPBF) 3D printer, Upwing has diminished the manufacturing time wanted to assist its SCS gasoline nicely deployment schedules.
3D printing has enabled the corporate to go from engineering design, to full compressor rotor meeting manufacturing in simply 10 weeks. Furthermore, checks which simulated the atmosphere of the gasoline compression course of highlighted the high-quality and sturdiness of the 3D printed elements.
“All of our work at Upwing is underscored by the idea that steady enchancment is at all times doable,” commented Robert McKeirnan, Vice President of Provide Chain and Exterior Manufacturing at Upwing Power.
“Our resolution to combine additive manufacturing makes us extra scalable and adaptable. It permits us to create elements that aren’t solely sturdy, however intricately designed and completed with the best degree of precision.”
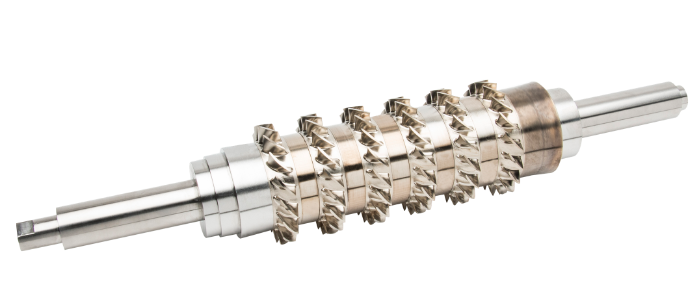
Optimizing SCS compressor module manufacturing
Manufactured from Inconel 718, Upwing’s proprietary SCS compressor module is designed to extend the manufacturing and recoverability of pure gasoline from current wells. To attain this, the SCS incorporates a multistage hybrid axial compressor, which will increase drawdown on the consumption and boosts strain on the discharge.
The corporate’s SCS compressor module incorporates an aerodynamic design to match well-specific stream parameters, permitting for optimum manufacturing achieve. In response to Upwing Power, the manufacturing of the compressor’s rotor design is very difficult as a result of its advanced floor geometries.
Along with notable lead time financial savings, Velo3D’s steel 3D printing know-how reportedly permits the creation of extra intricate designs than typical manufacturing strategies. What’s extra, the 3D printed elements characteristic geometric and supplies advantages, leading to improved efficiency and elevated half lifecycle.
Tensile testing has demonstrated that additively manufactured Inconel 718 elements meet ASTM F3055 requirements. Downhole compressor-specific necessities are additionally reportedly met by 3D printed Inconel 718.
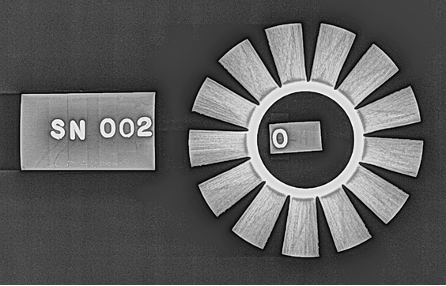
Through the SCS improvement course of, the mechanical properties of 3D printed elements had been in comparison with these produced by means of machined billet, a typical industrial manufacturing technique. Right here, varied checks simulating circumstances discovered within the SCS’s gasoline compression course of had been performed.
Each 3D printed and machined billet-produced elements had been examined at rotational speeds of 55K RPM or greater, the operational overspeed for the SCS. Detailed inspection was then carried out on the elements. This included using dye penetrant to reveal floor defects, steadiness checks, and dimension precision inspections. Lastly, a spin-to-burst take a look at was performed to validate the integrity of every manufacturing technique.
In the end, the additively manufactured elements efficiently endured the usual working circumstances of the gasoline compression course of, exceeding overspeed circumstances by 2.1 instances earlier than failure.
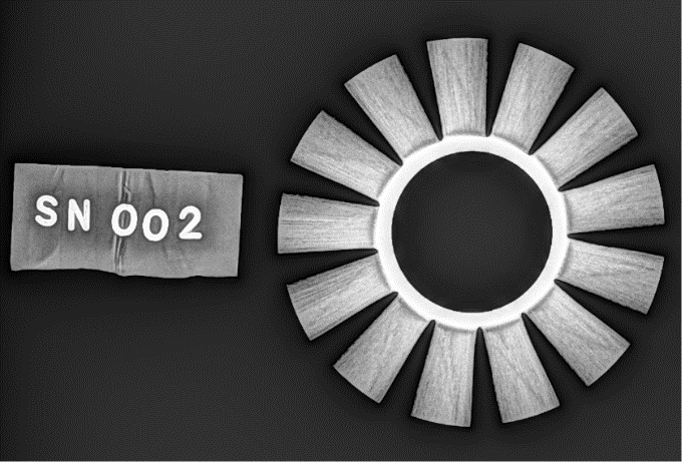
Bolstering the oil and gasoline sector with AM
Using additive manufacturing throughout the oil and gasoline trade is rising, with corporations leveraging industrial 3D printing for a variety of functions.
Certainly, this isn’t the primary time that know-how from Velo3D has been utilized inside this sector. Earlier this yr, Schoeller-Bleckmann Oilfield Know-how (SBOT) bought a Velo3D Sapphire XC large-format 3D steel printer.
Calibrated for Inconel 718, the Sapphire XC is getting used to fulfill rising demand for 3D printed elements from SBOT’s clients. Because of its geometric design flexibility, Velo3D’s 3D printer facilitates the manufacturing of intricate, mission crucial elements for oil and gasoline functions.
Elsewhere, UK industrial valve provider KOSO Kent Introl (Kent Introl) collaborated with international engineering agency Renishaw to evaluate the benefits supplied by additive manufacturing in oil and gasoline.
Kent Introl put in a Renishaw RenAM 500Q Flex 3D printer at its Brighouse, West Yorkshire HQ. The corporate claims to be the primary UK producer within the oil and gasoline trade to undertake additive manufacturing. The steel 3D printer is at present getting used for R&D functions, in addition to the fast manufacturing of elements to shortly meet buyer calls for.
Subscribe to the 3D Printing Trade publication to maintain updated with the newest 3D printing information. You too can comply with us on Twitter, like our Fb web page, and subscribe to the 3D Printing Trade Youtube channel to entry extra unique content material.
Are you curious about working within the additive manufacturing trade? Go to 3D Printing Jobs to view a choice of accessible roles and kickstart your profession.
Featured picture reveals Oil drilling in an oil area. Photograph through UTSA.
[ad_2]