
[ad_1]
Researchers have developed a brand new methodology to make sure uniform shrinkage in 3D printed micro and nanostructures, utilizing two-photon polymerization lithography (TPL). The staff, led by Professor Joel Yang from the Singapore College of Know-how and Design (SUTD), collaborated with the Industrial Know-how Middle of Wakayama Prefecture in Japan. Their course of employs a layer of poly(vinyl alcohol) (PVA) on the printing substrate, enabling the switch of 3D printed elements onto a separate substrate for managed discount. This system addresses the problem of non-uniform shrinkage and expands the potential purposes of TPL.
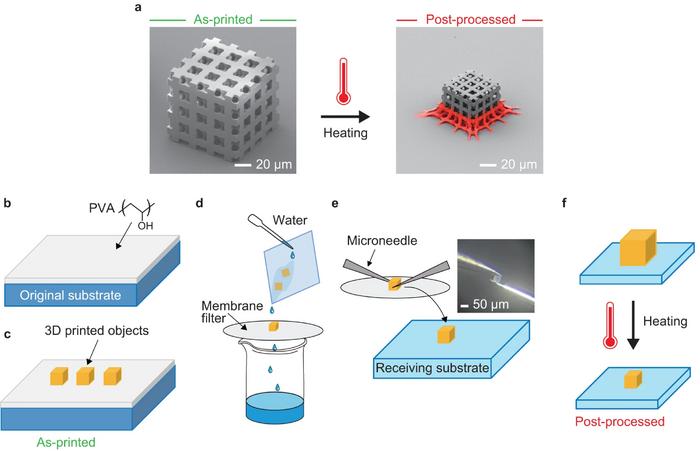
The analysis, printed in Nature Communications, showcases the profitable utility of this methodology on advanced geometries. The unfastened attachment of the buildings to the brand new substrate permits for uniform shrinkage throughout heating, avoiding distortions. This method not solely overcomes limitations in decision and materials rigidity but in addition permits for the combination of microscopic 3D printed elements with different gadgets or substrates unsuitable for TPL.
This system opens up new prospects, corresponding to creating supplies that change colours in response to lighting situations, helpful in anti-counterfeiting. It additionally guarantees developments in manufacturing intricate warmth sinks for high-performance electronics and allows the creation of mechanical elements, optical components, and acoustic gadgets with excessive precision.
The staff plans to increase the applying of their method to supplies with increased refractive indices for improved photonic crystals, enhancing applied sciences in lasers, imaging programs, and optical sensors. They’re additionally refining the management of spacing in printed buildings for full-color, 3D fashions that manipulate gentle exactly.
You’ll be able to learn the analysis paper titled “Decide and place course of for uniform shrinking of 3D printed micro- and nano-architected supplies” over at this hyperlink.
Come and tell us your ideas on our Fb, X, and LinkedIn pages, and don’t overlook to enroll in our weekly additive manufacturing e-newsletter to get all the newest tales delivered proper to your inbox.
[ad_2]